Research
Thermoplastic composites are an advanced material with a big future ahead in aerospace, to make products lighter, stronger, more cost-efficient and sustainable. We are a specialist research center with a clear focus on thermoplastic composites and their manufacturing processes. Generic research activities are captured by a roadmap that is defined by the industrial partners within their membership.
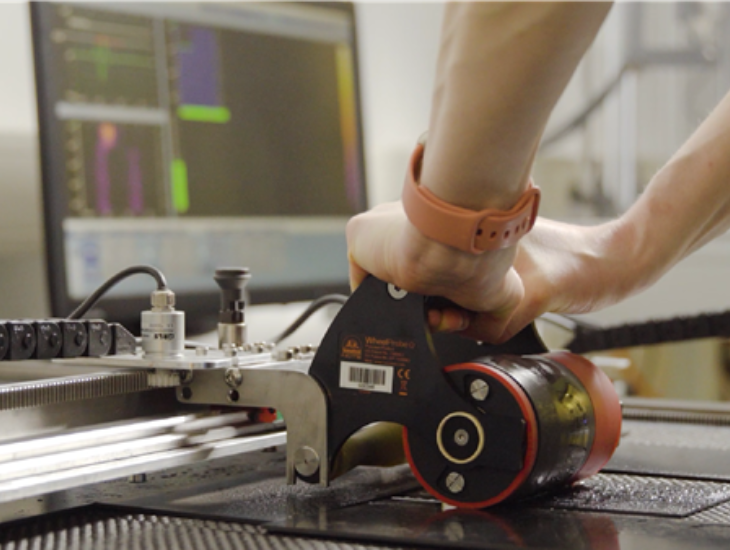
Our research roadmap
Our research roadmap is aimed at generating the fundamental knowledge that supports the design of thermoplastic composite structures, the optimization of existing and new manufacturing processes and the development of sustainable process chains. We perform specific, exclusive research for members and non-members besides the roadmap. The activities can range from short term engineering work, training and consultancy to longer research projects.
"I would describe research conducted at TPRC as World Class."
#TPRCminds series
Our TPRC minds series introduces you to the people behind our success.
Who are they? What is their background? What drives them and what do they dream about? How do they look at the future of thermoplastic composites?