Cost-effective manufacturing of large aerospace structures
Thermoplastic composites are very attractive for manufacturing large structures using out-of-autoclave consolidation technologies combined with welding. Large stiffened panels are ideally produced by joining rapidly formed ribs to skins made with the Advanced Fiber Placement process.
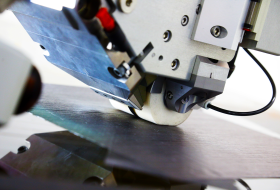
Laser-assisted Advanced Fiber Placement
The laser-assisted automated fiber placement (AFP) process enables highly tailored lay-ups in near-net- shaped parts, while reducing the amount of manual labor. The TPRC assists with:
- In-situ consolidation of new and existing tapes
- Process simulation
- Material characterization and optimization
- Demonstrator parts
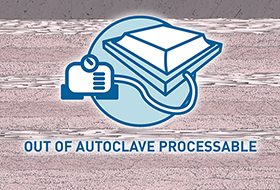
Out-of-autoclave consolidation
Manufacturing of large parts without using an autoclave has become more and more attractive with the recent development of new thermoplastic composite materials. The TPRC is working on:
- Consolidation with vacuum-only
- Virtual process tool
- Material evaluation for out-of-autoclave consolidation
- Technology demonstration
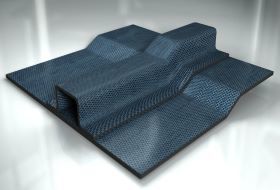
Joining of thermoplastic composites
Thermoplastic composites can be joined by welding, in addition to traditional technologies such as mechanical fastening and adhesive bonding. Automated welding is fast, clean and requires no additional materials in most cases. The topics that the TPRC specializes on are:
- Coupon level welding using induction, ultrasonic and resistance heating
- Bond strength evaluation
- Process optimization using simulation tools
- Material characterization