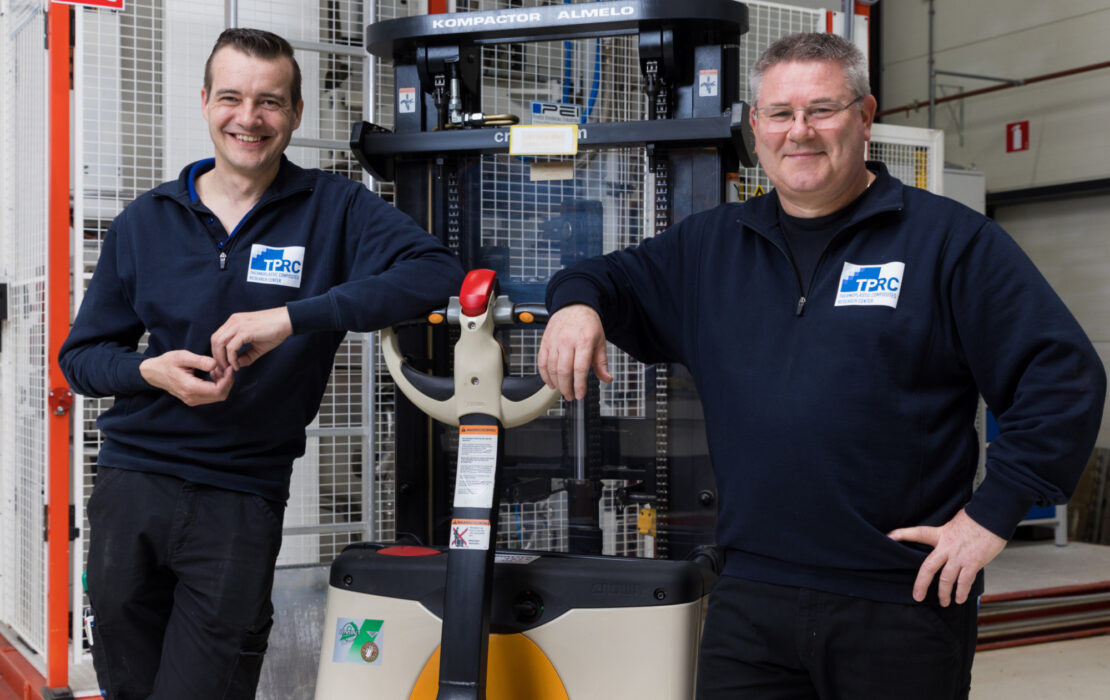
About us
As a unique research center for thermoplastic composites, we focus on enabling the use of the thermoplastic composite technology in large volume applications while also promoting the widespread adoption of these materials through fundamental knowledge development.
Meet the teamDedicated research center for thermoplastic composites
Although specific thermoplastic composite components and substructures are already being applied commercially, there is limited understanding of complex physical mechanisms and phenomena in the use and manufacturing of thermoplastic composites. The technological challenges faced by industry can be found at various technology and manufacturing levels of readiness. In our research center, an enthusiastic and committed team of experts work together to increase knowledge of these materials, their behavior and processing technologies. Our expertise and lab are available for members and non-members. We offer training, consultancy and smaller-scale, application-oriented research projects.
TPRC highlights
In just over 10 years, we have grown into a unique and worldwide research center for thermoplastic composites. On the occasion of our tenth anniversary, we organized the Future of Thermoplastic Composites conference in October 2019. We have now grown into an international consortium. The unique thing about it is that the entire value chain is represented. Expanding the consortium will remain important for the industrial application of thermoplastic composites.
Our expertise explained in the TPRC Talks series
The TPRC Talks are a live, online talk show in which we invite you along into our consortium and the world of thermoplastic composites. In these four episodes, studio guests talked about our mission, the lab, and what our research is currently focusing on. Our valued partners also explained the importance of thermoplastic composites research and the benefits of working closely together with the partners within the consortium. And our researchers explained their research, such as stamp forming and welding. We are thankful for the many people who helped us realize and participated in the TPRC Talks.
The benefits of composites
Thermoplastic composites are advanced materials with a big future ahead in aerospace, to make products lighter, stronger, more cost-efficient and sustainable. The benefits of composites in aircraft are explained in several tutorials by Arnt Offringa, Head of Thermoplastic Composites Technology, Fokker, GKN Aerospace. Arnt is a highly valued ambassador of the TPRC.
Valuable networks
CompositesNL
CompositesNL represents the interests of all organizations in the Netherlands that are involved in the development, manufacture, maintenance, and reuse of products in which composite technology has played a part.
Membership of CompositesNL is valuable, as it brings thermoplastic composites to the attention of parties that could benefit from a more sustainable society. In addition, they represent the entire composites sector towards governments, so that the sector can be put more firmly on the map.
TPC NL - Smart Industry Fieldlab
TPC NL, the Smart Industry Fieldlab for ThermoPlastic Composites, aims at making thermoplastic composites work for local and (inter-)national industry and thus enhance their economic impact.
TPC NL is a joint development of the TPAC, ThermoPlastic composites Application Center, and the TPRC, ThermoPlastic composites Research Center, both based in Enschede. This offers a sound base on thermoplastic composite knowledge and expertise and a direct link with industry, both large enterprises and SMEs, and universities.
Meet the team!
With our experienced and multidisciplinary team and the experts from partners, we have the capabilities to tackle any problem you may have with regard to thermoplastic composites. Within the TPRC, renowned experts in the field of thermoplastic composites work together to increase knowledge of these materials and their behavior, product design and processing technologies.
Who are the people behind the success of the TPRC? What drives them and what do they dream about? How do they look at the future of thermoplastic composites?
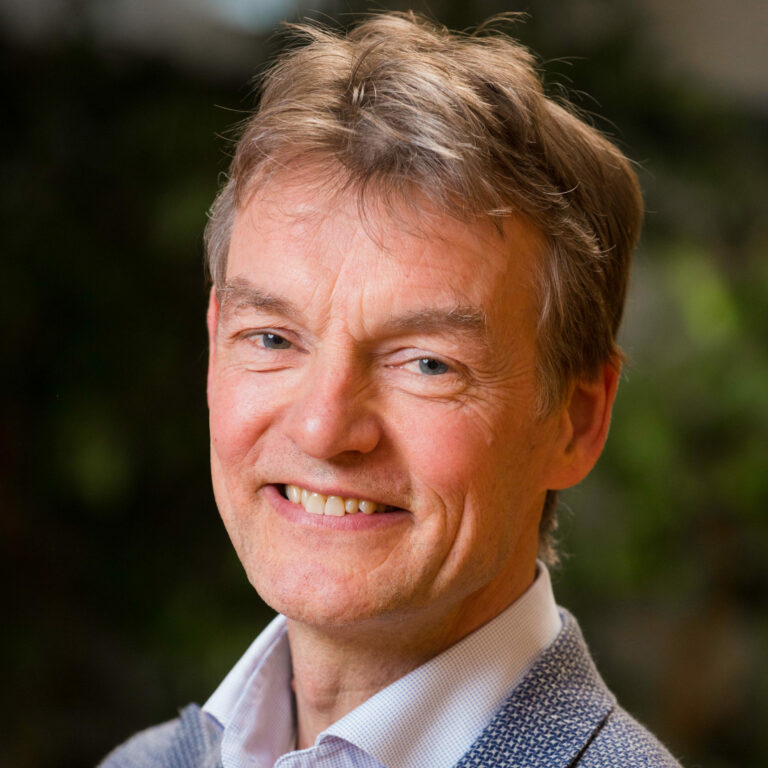
Scientific Director
Remko Akkerman
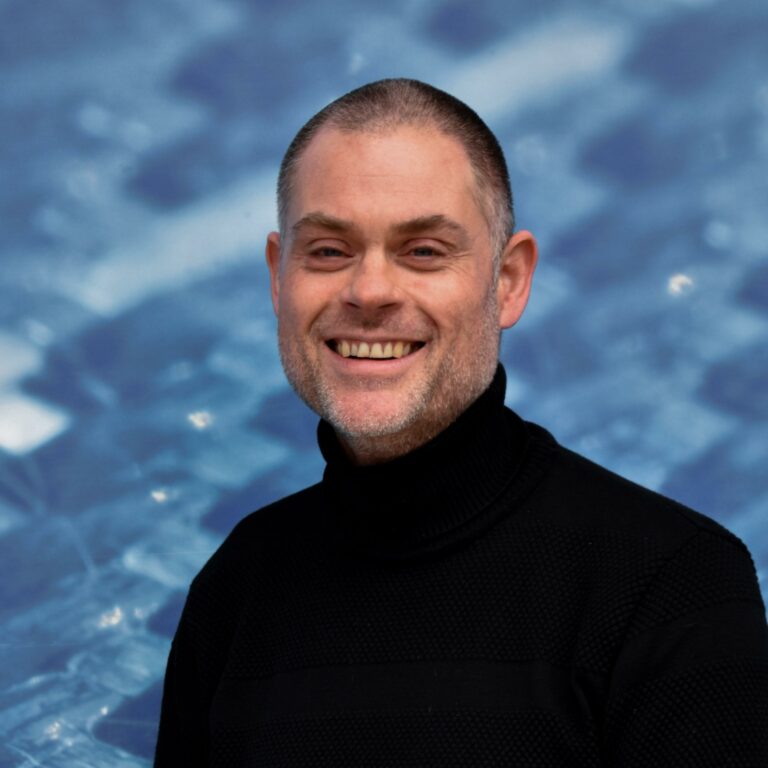
General Manager
Sebastiaan Wijskamp
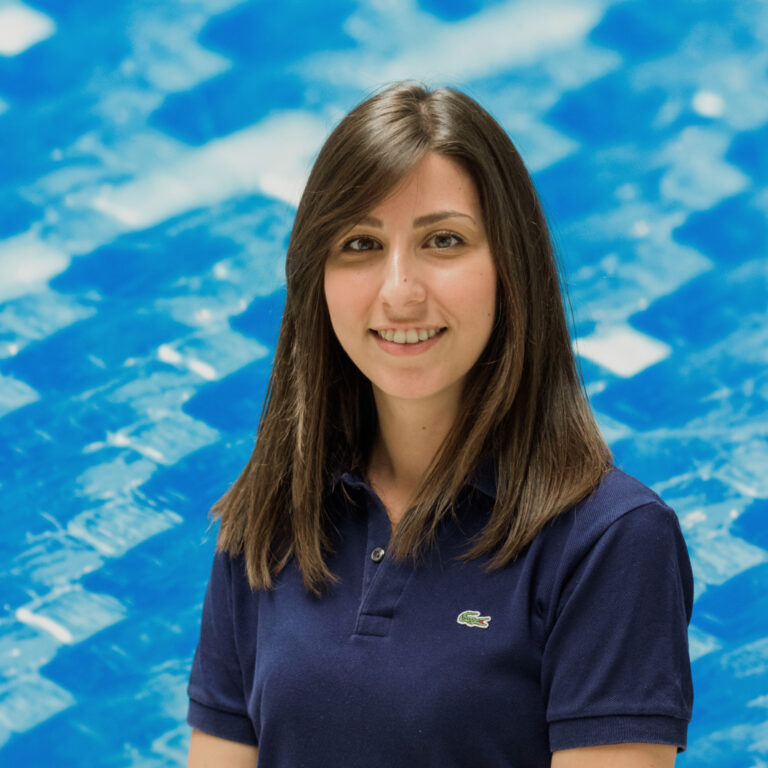
Technical Director
Vanessa Marinosci
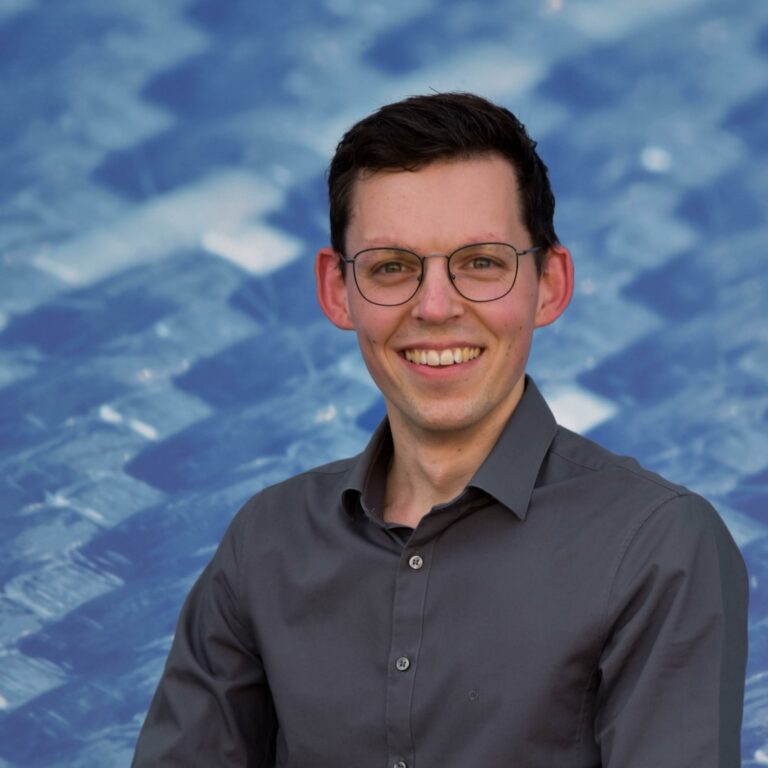
Senior Research Associate | Business Developer
Rens Pierik
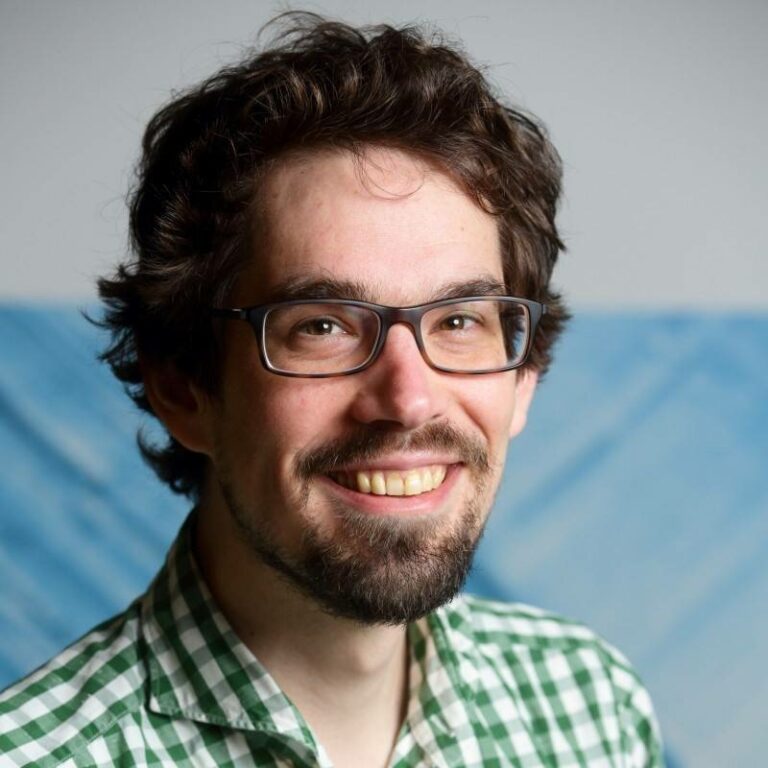
Senior Research Associate
Wouter Grouve
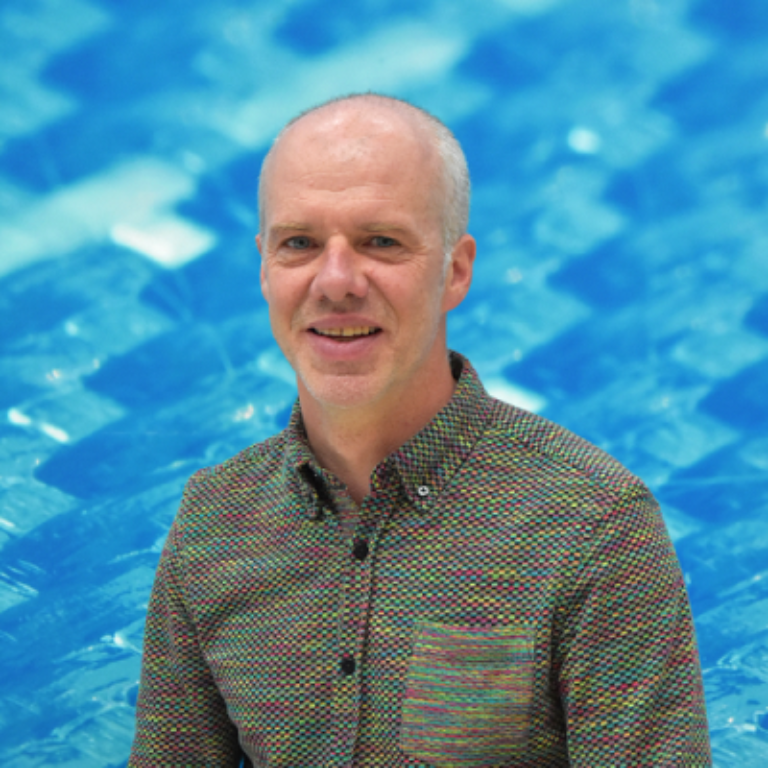
Senior Research Associate
Laurent Warnet
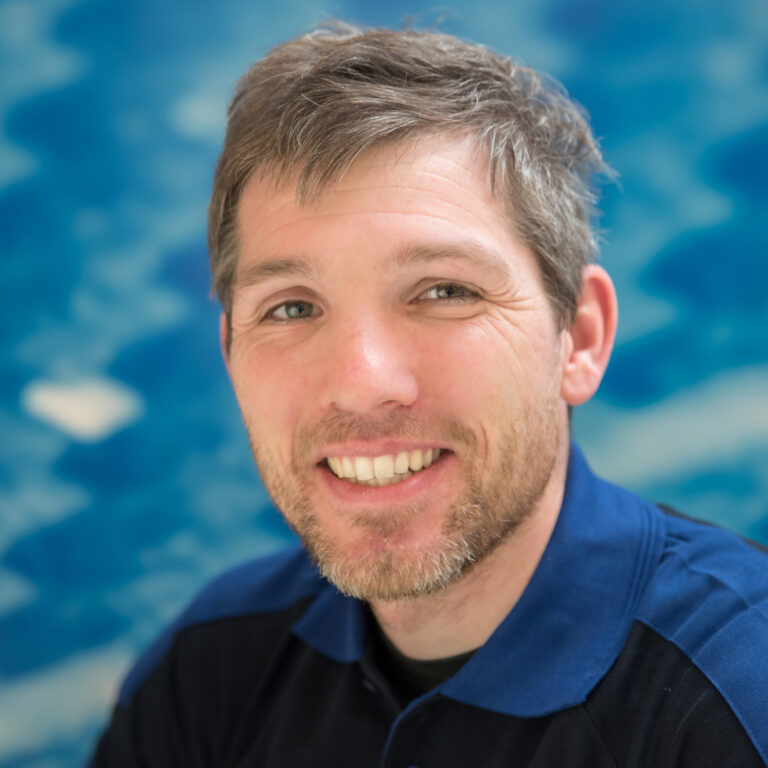
Senior Research Associate
Ulrich Sachs
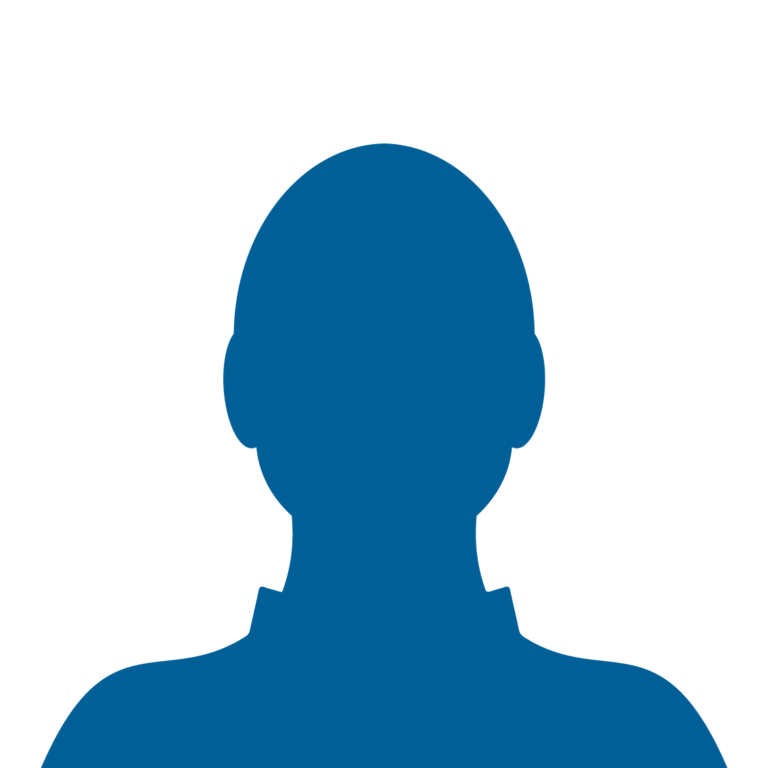
Senior Research Associate
Edwin Klompen
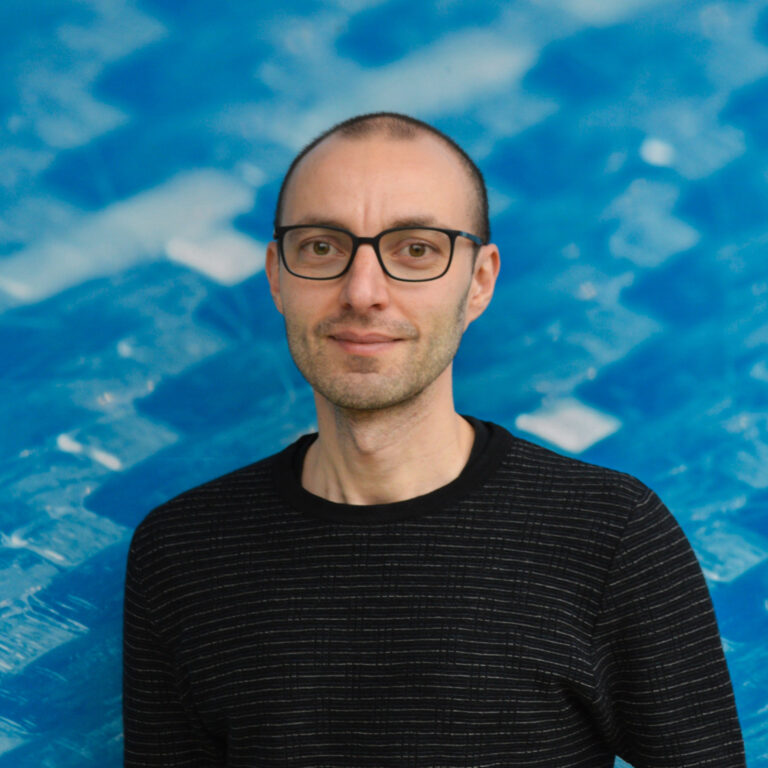
Senior Research Associate
Francesco Rondina
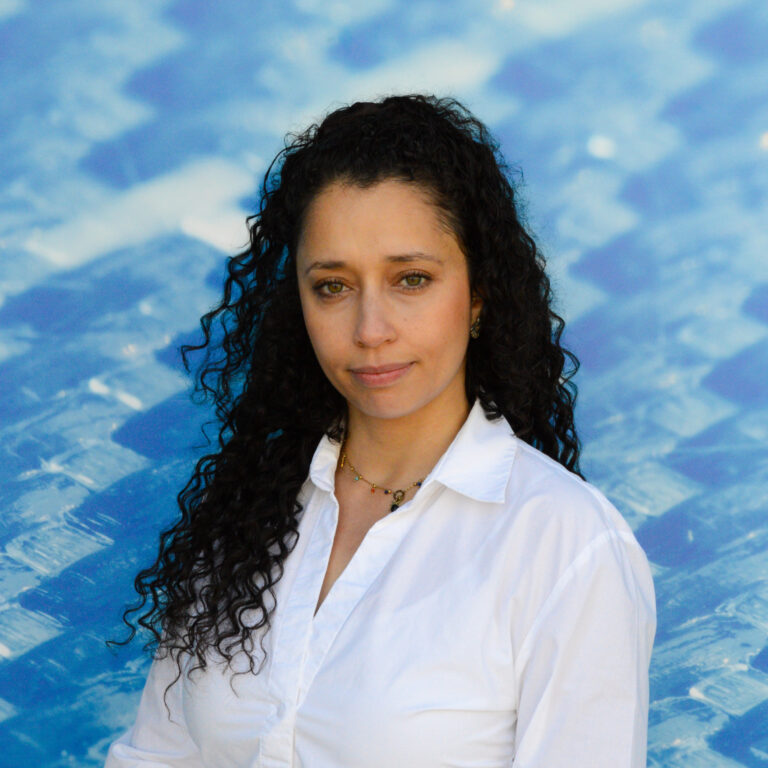
Senior Research Associate
Luiza Melo de Lima
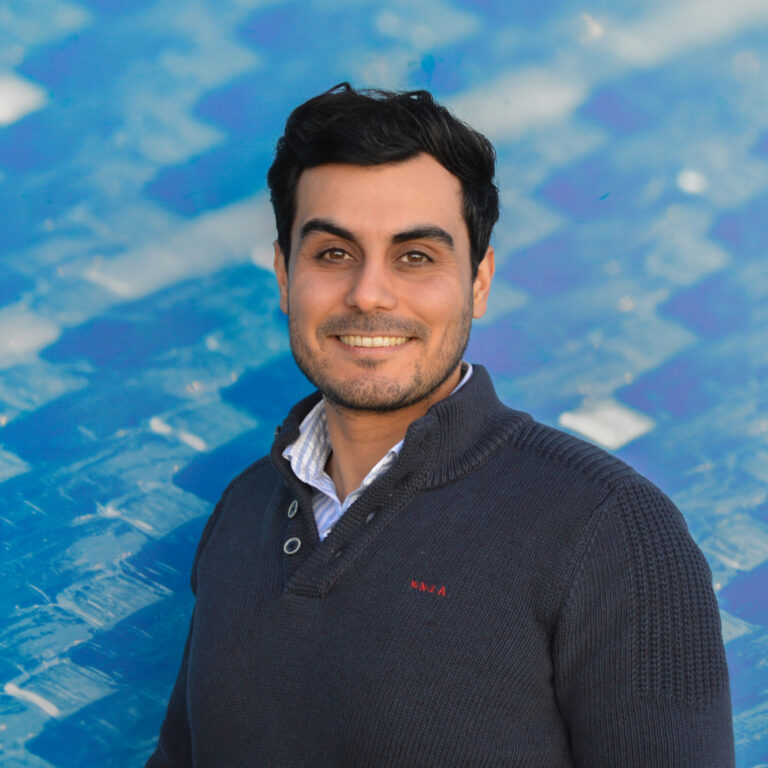
Senior Research Associate
Vahid Rezazadeh
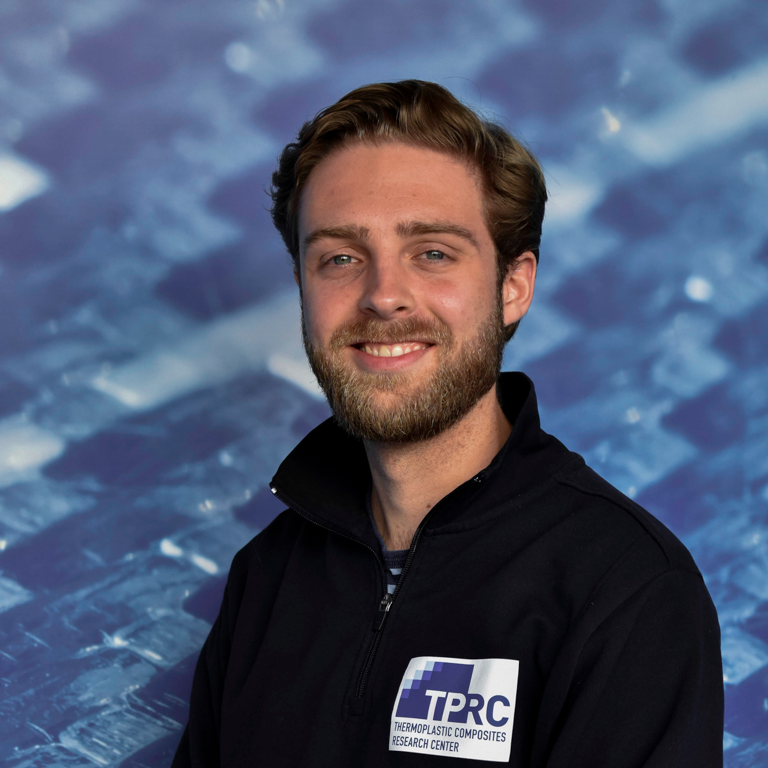
Senior Research Engineer | Lab Manager
Lars Niens
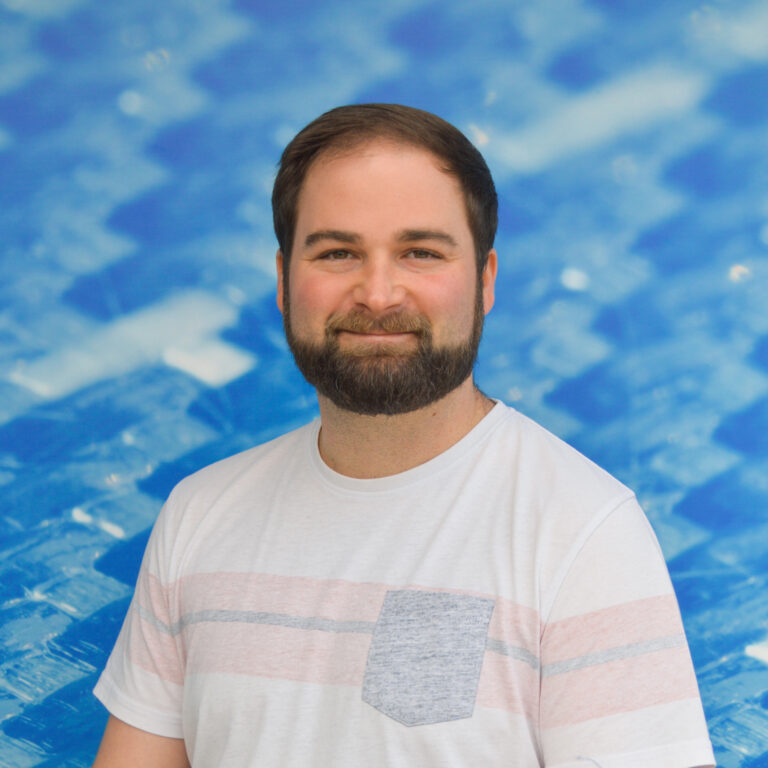
Engineering Manager
Lazlo Giesgen
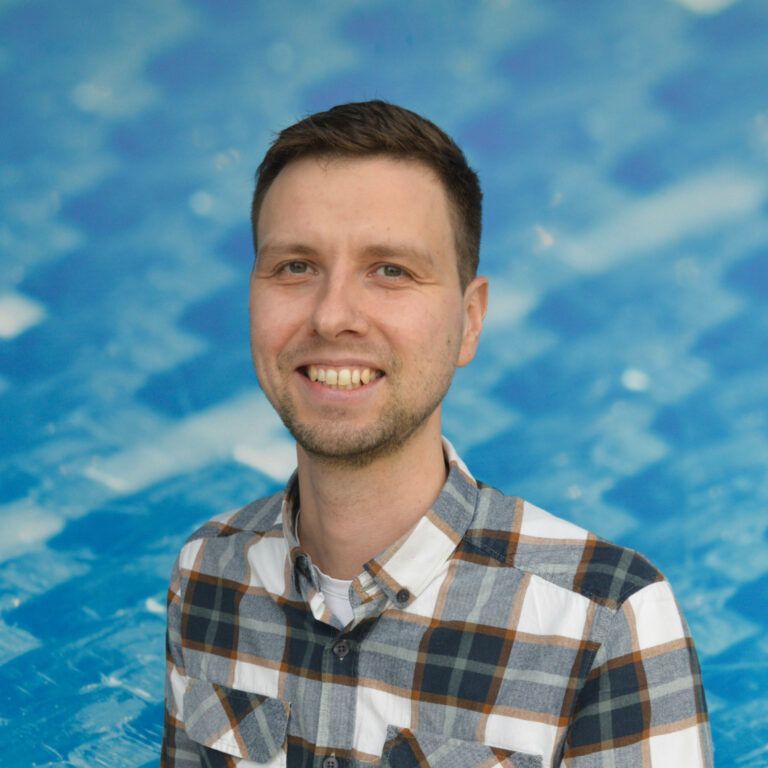
Researcher
Marten van der Werff
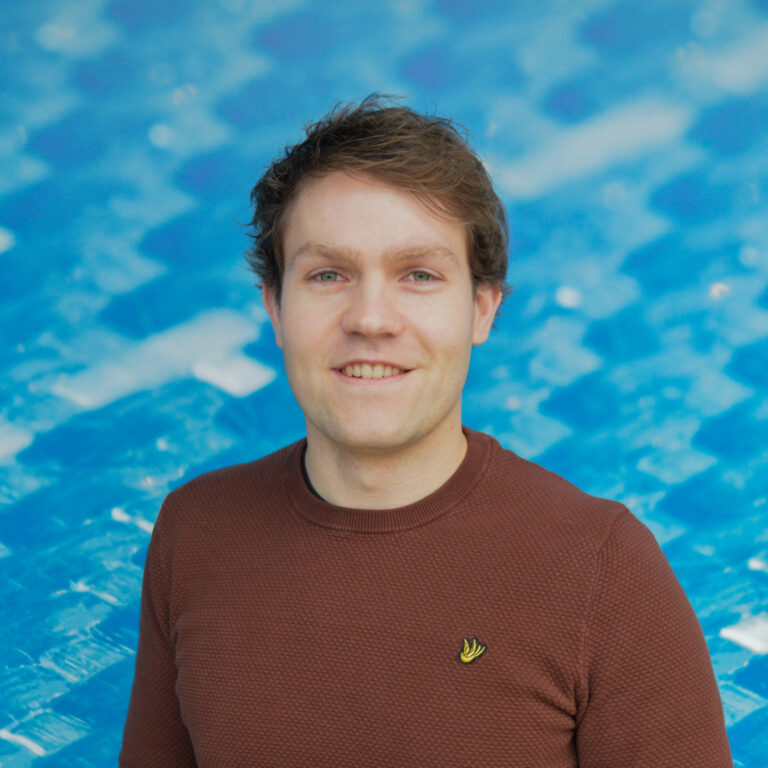
Research Engineer
Joran Geschiere
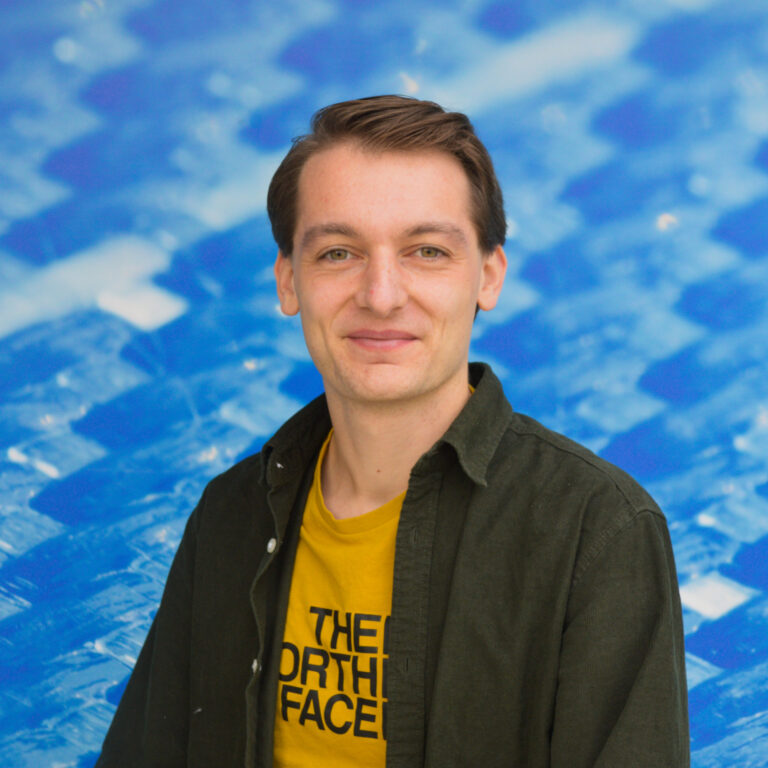
Research Engineer
Arthur Haverkort
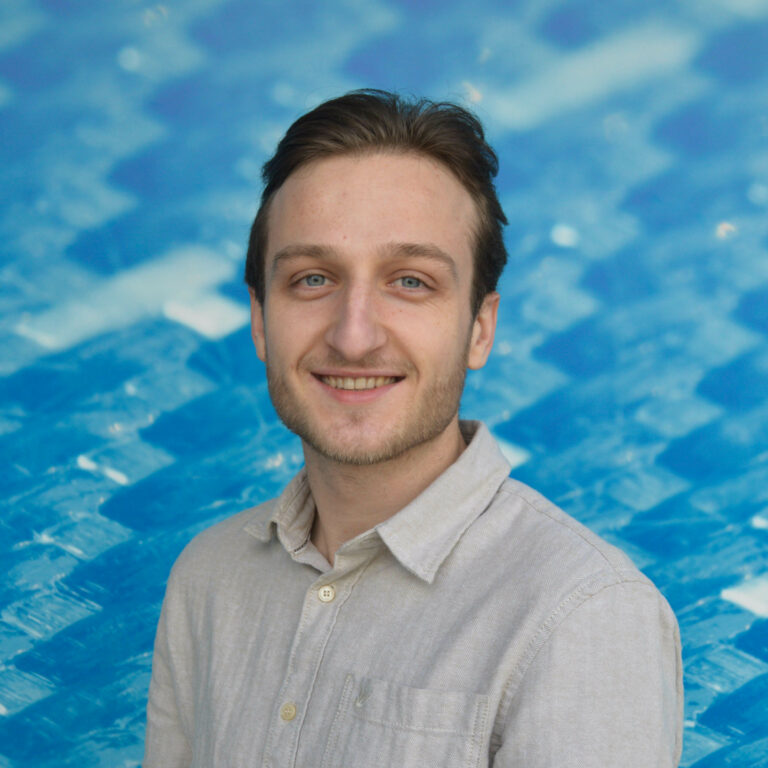
Research Engineer
Mats Baten
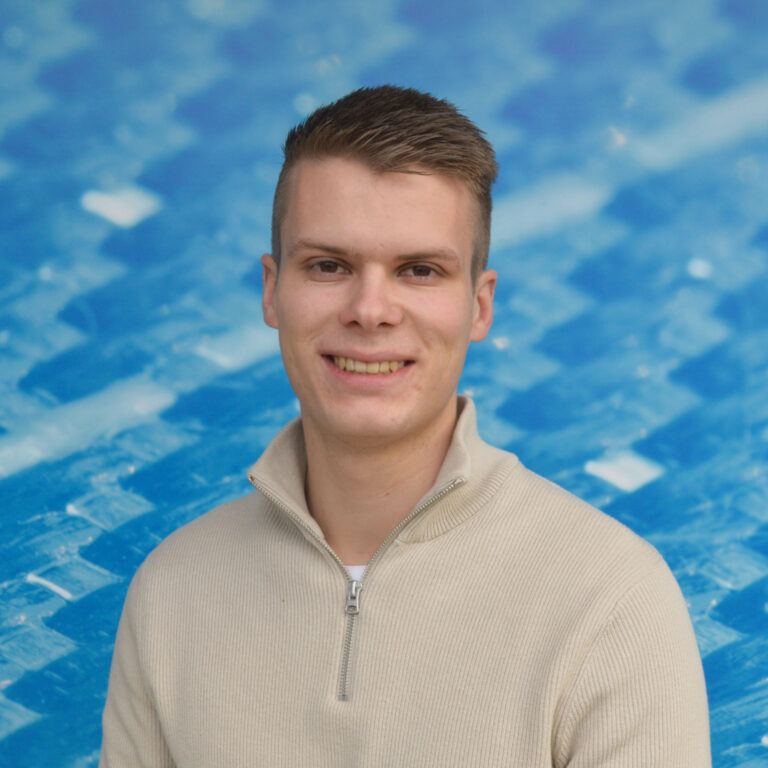
Research Engineer
Luuk Bolster
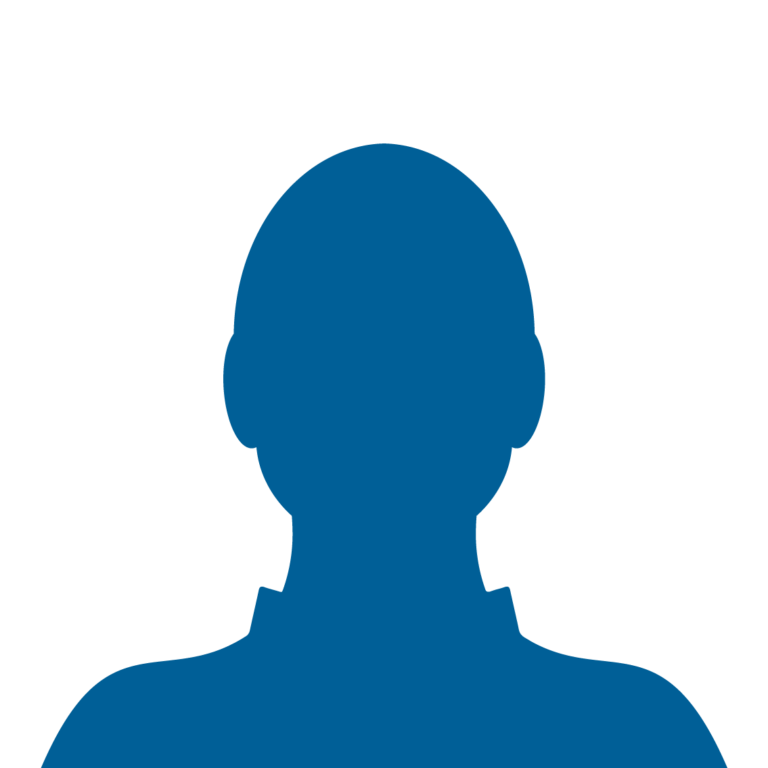
Research Engineer
Timo Westerveld
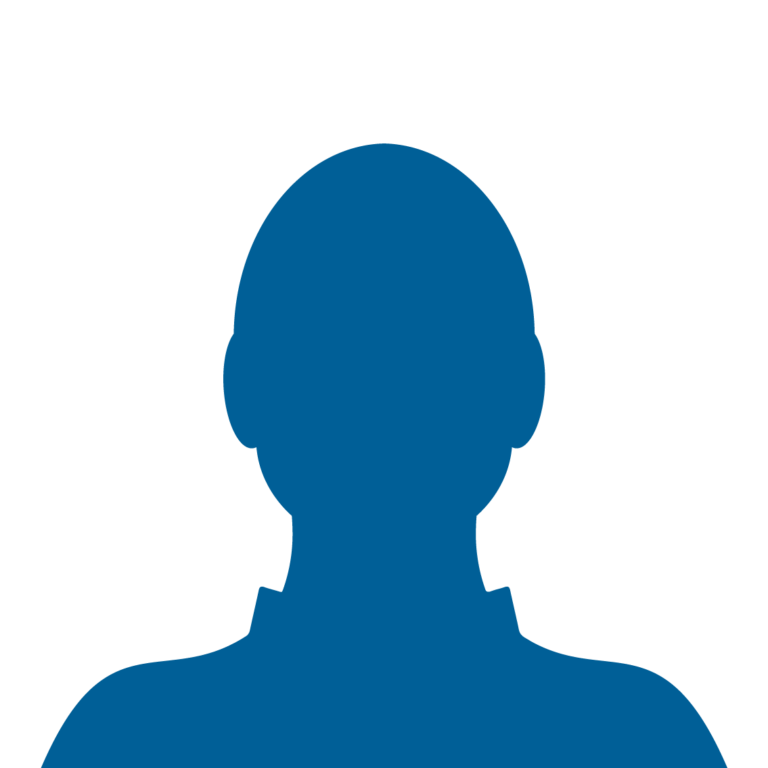
Research Engineer
Teun Stevens
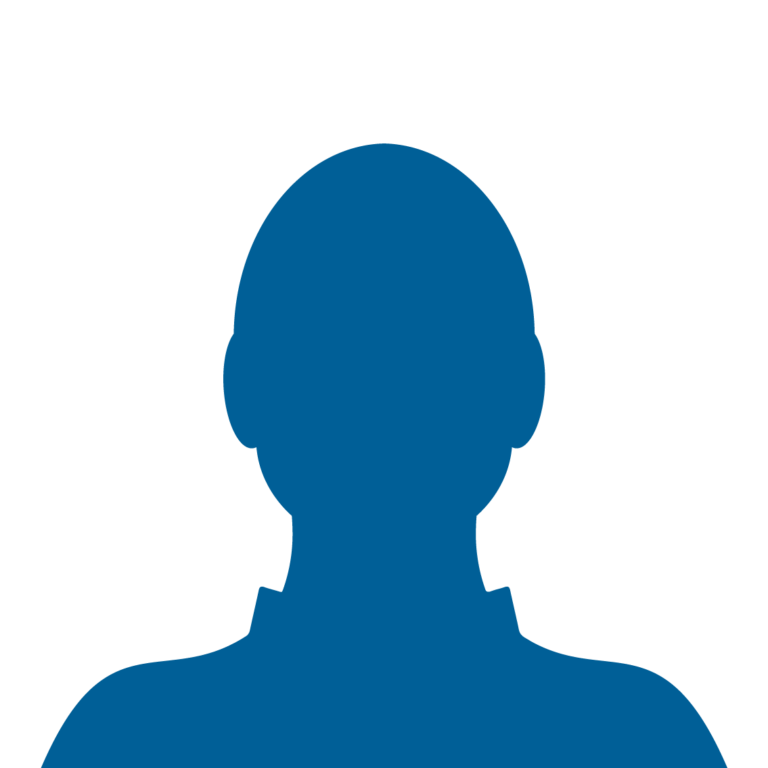
Senior Research Engineer
Ceren Yildirim
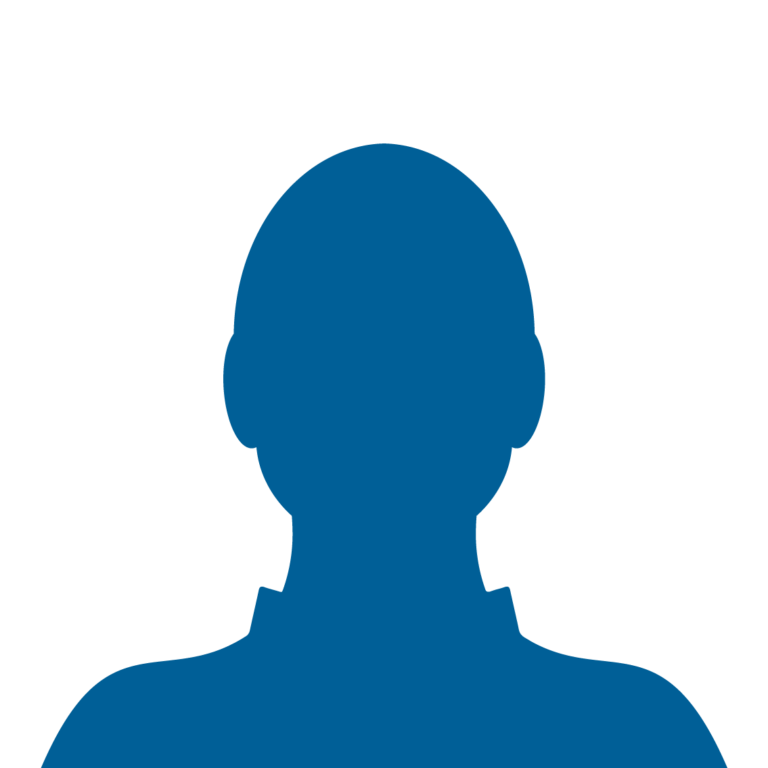
Research Engineer
Arastu Sharma
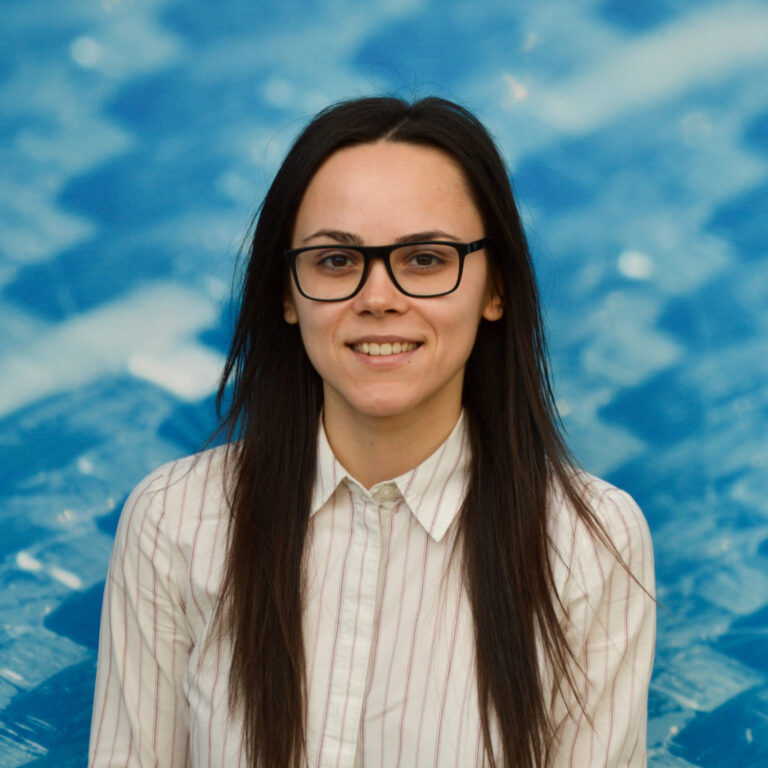
Research Engineer
Victoria Ciobãnescu
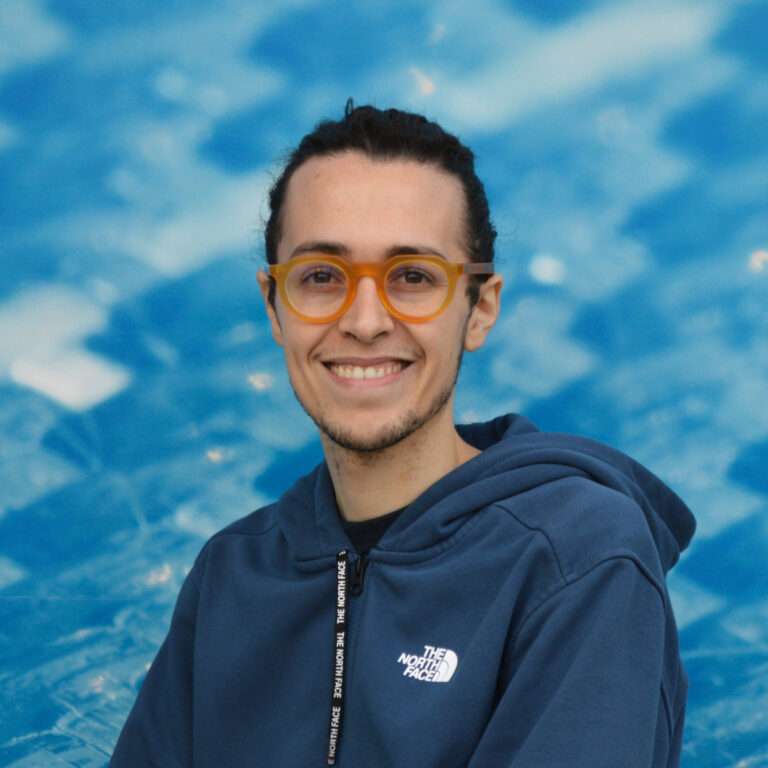
Research Engineer
Filippo Maggioli
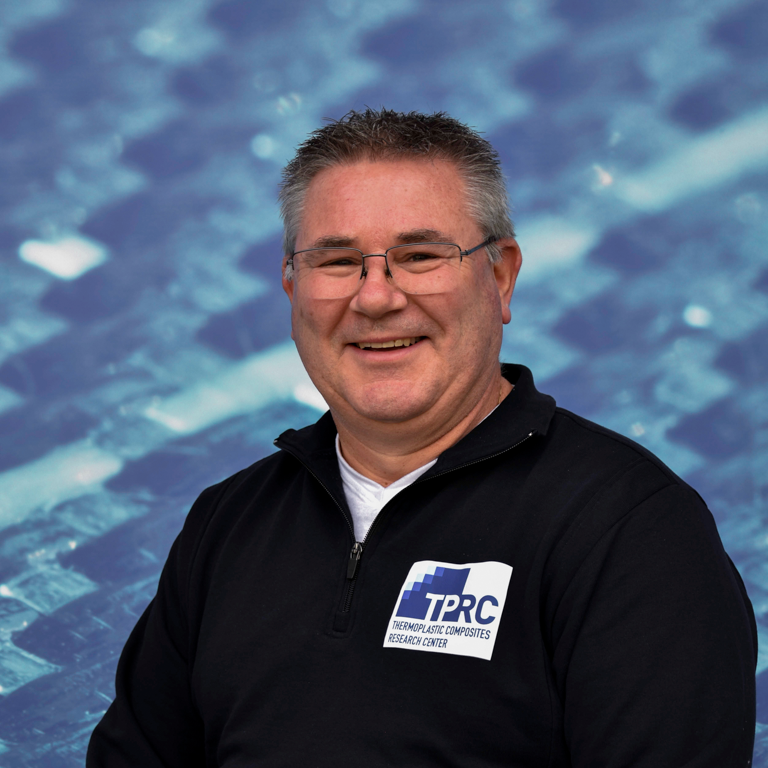
Research Technician
Martin Hartman
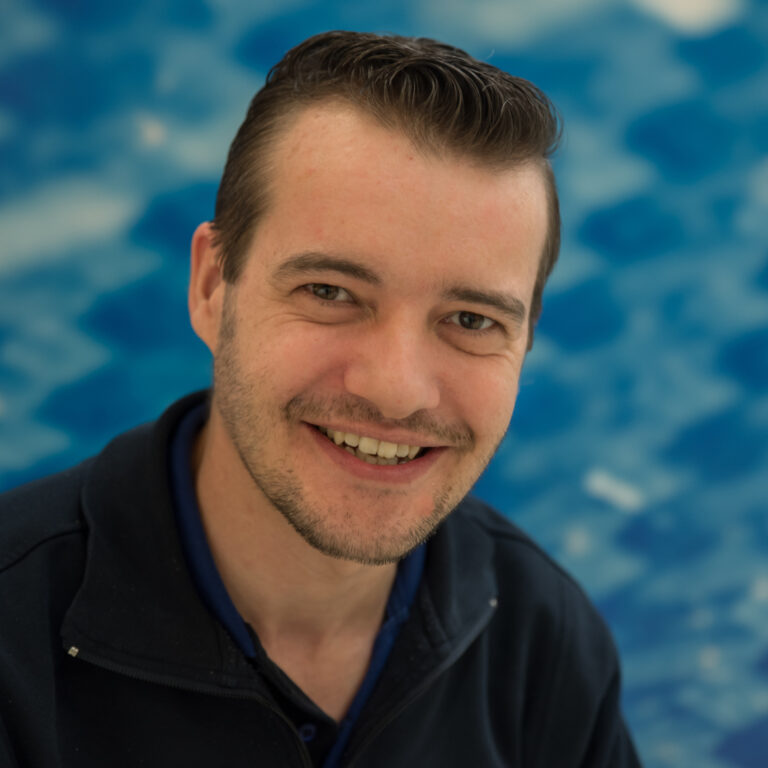
Research Technician
Edwar Boer
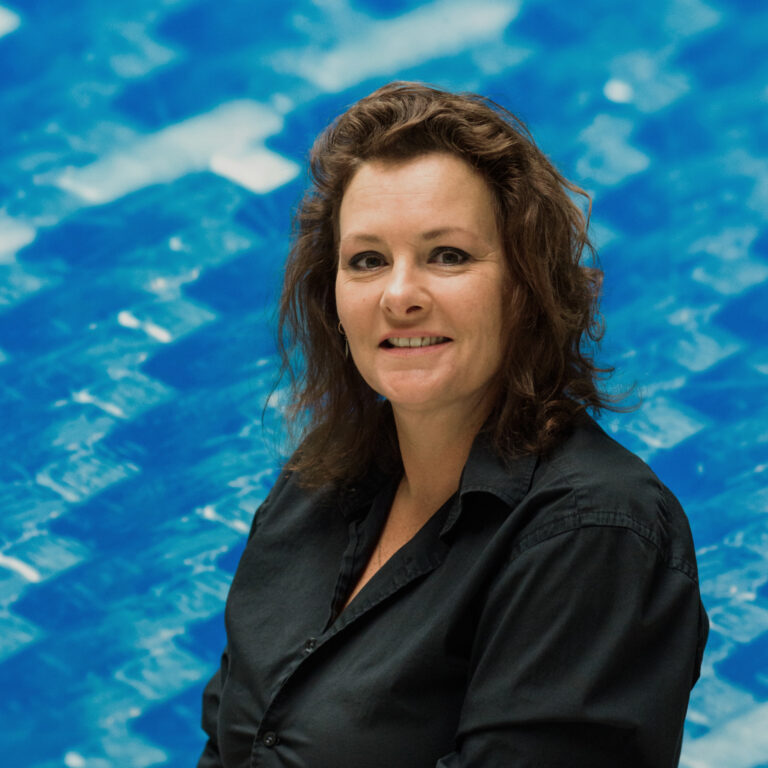
Procurement Manager | Prevention
Selma Adam-Kalee
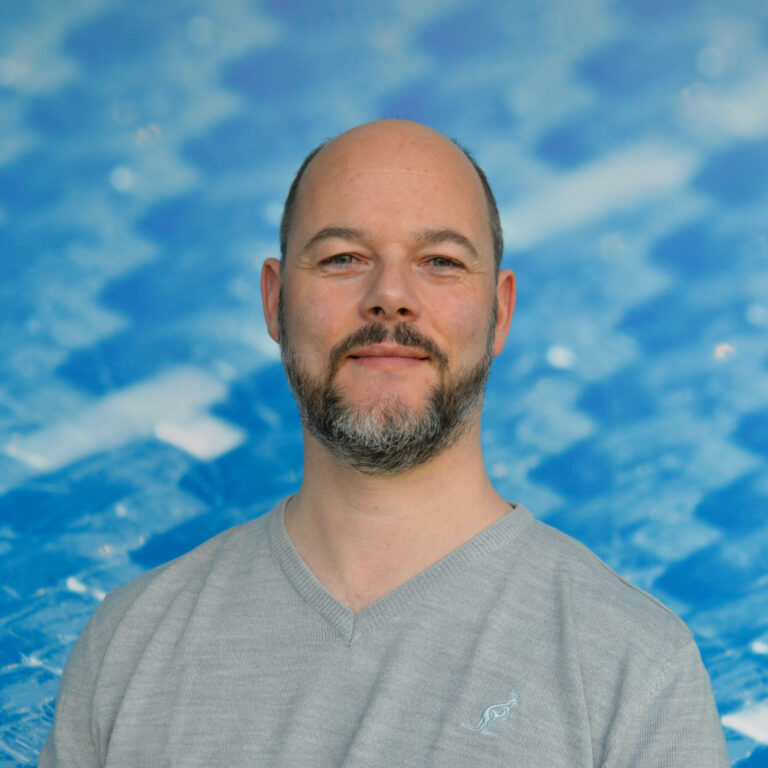
Financial Controller
Matthijs van der Velden
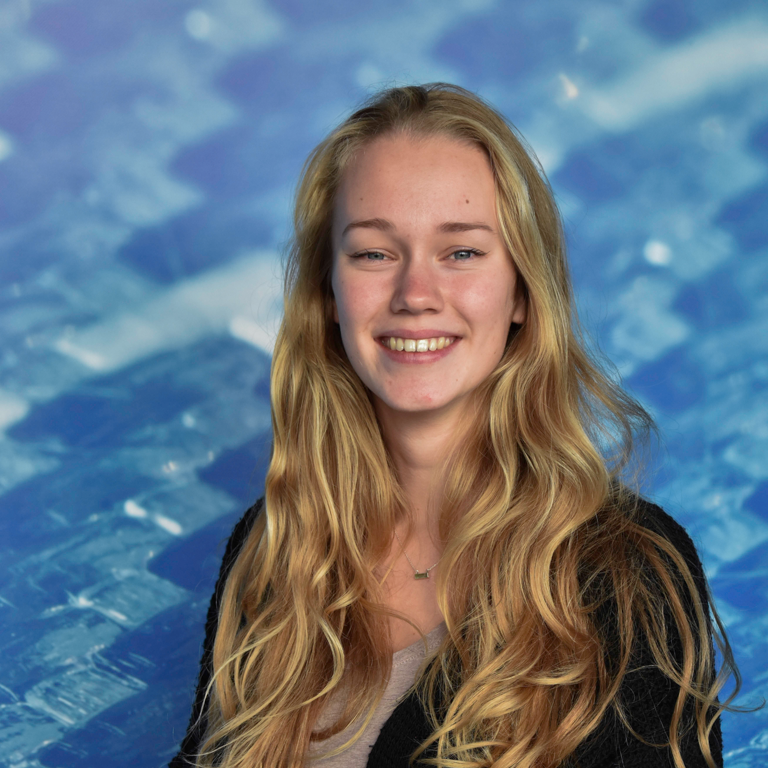
Marketing & PR Manager
Hilda Hoekstra
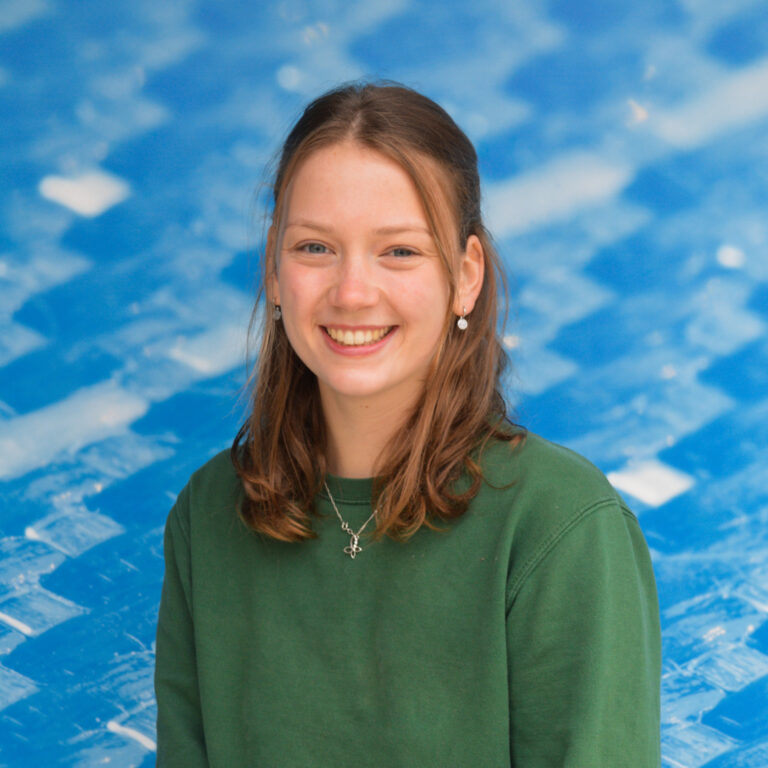
Marketing & PR Assistant
Britt van Slooten
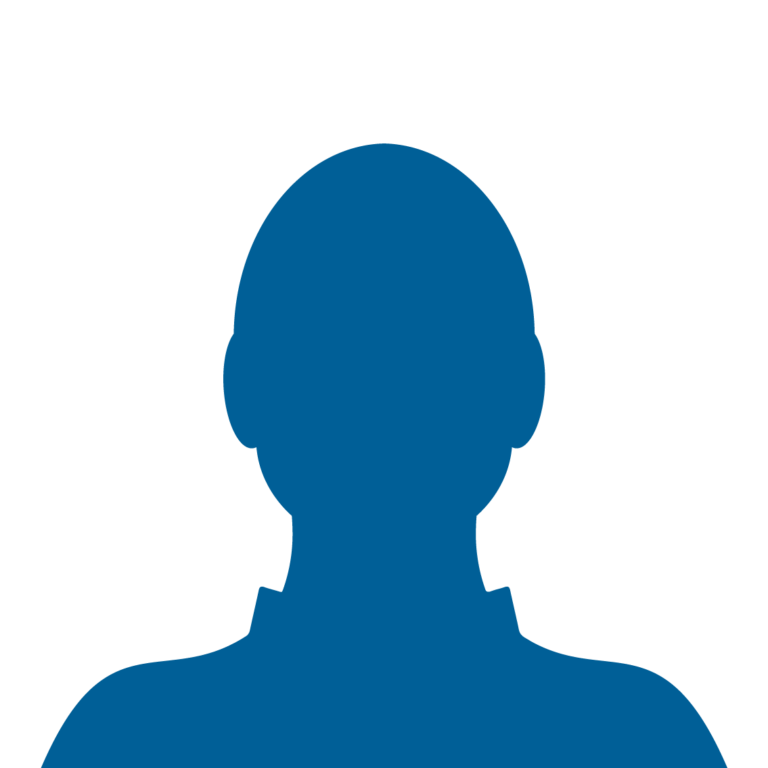
Marketing & PR Assistant
Maya Schuurmans
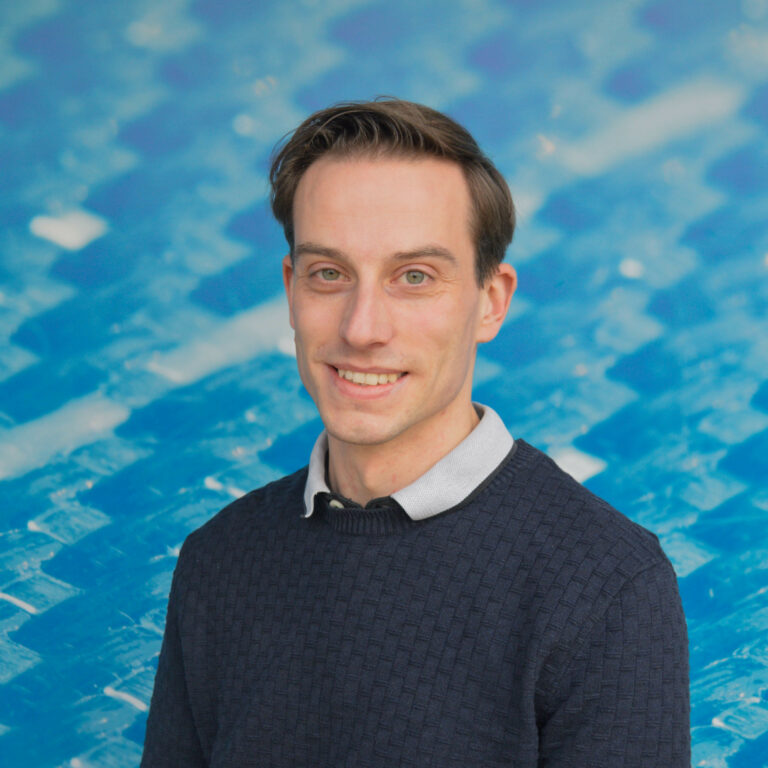
PhD Researcher
Tom Asijee
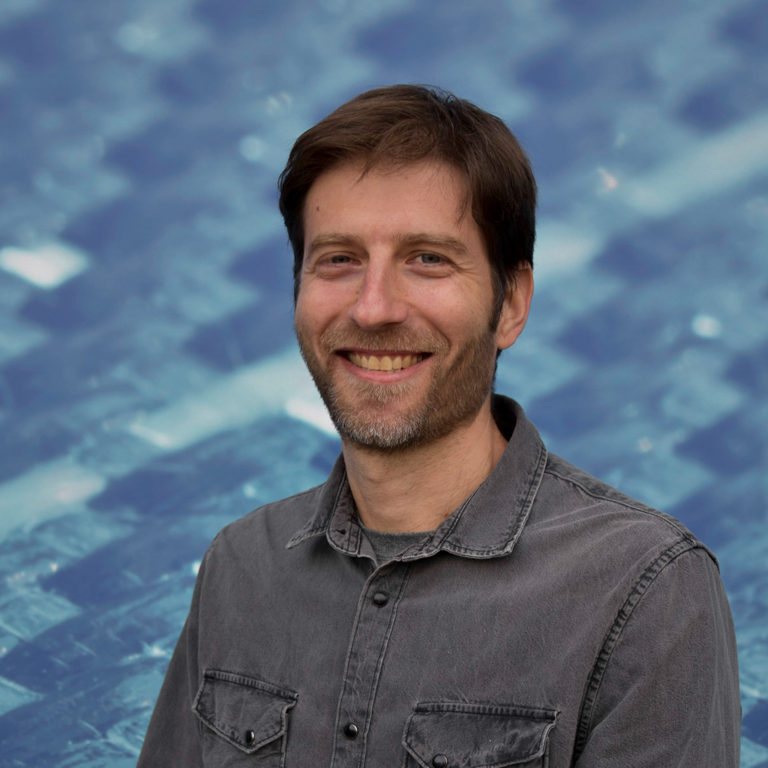
PhD Researcher
Liran Katz
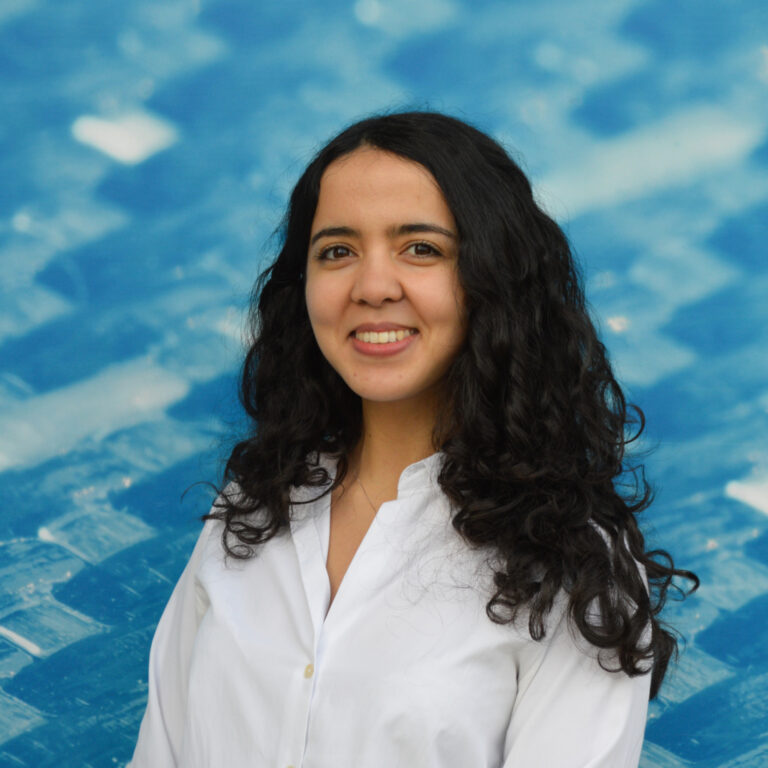
PhD Researcher
Sabrine Bentalib
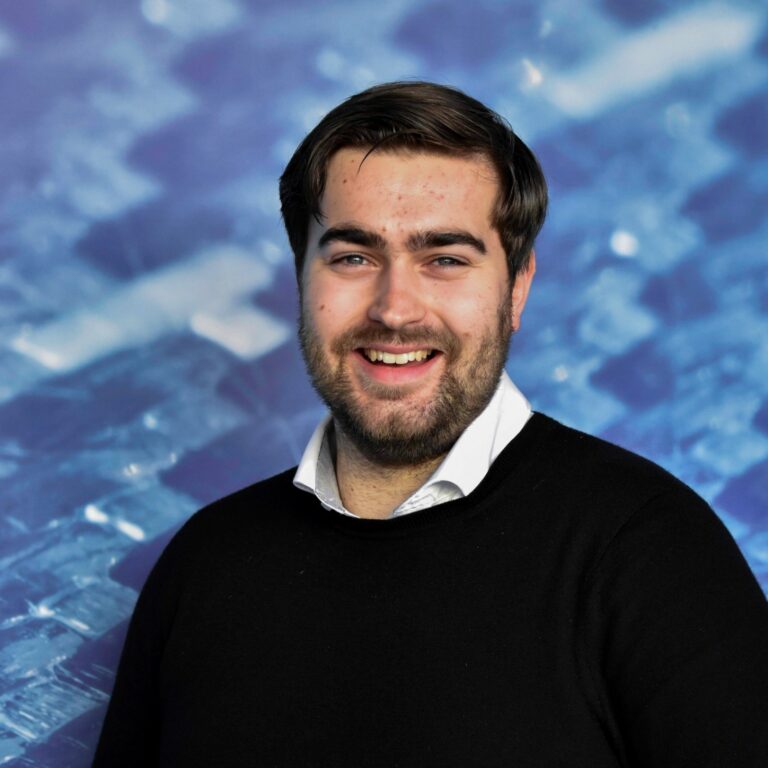
PhD Researcher
Gerben Bieleman
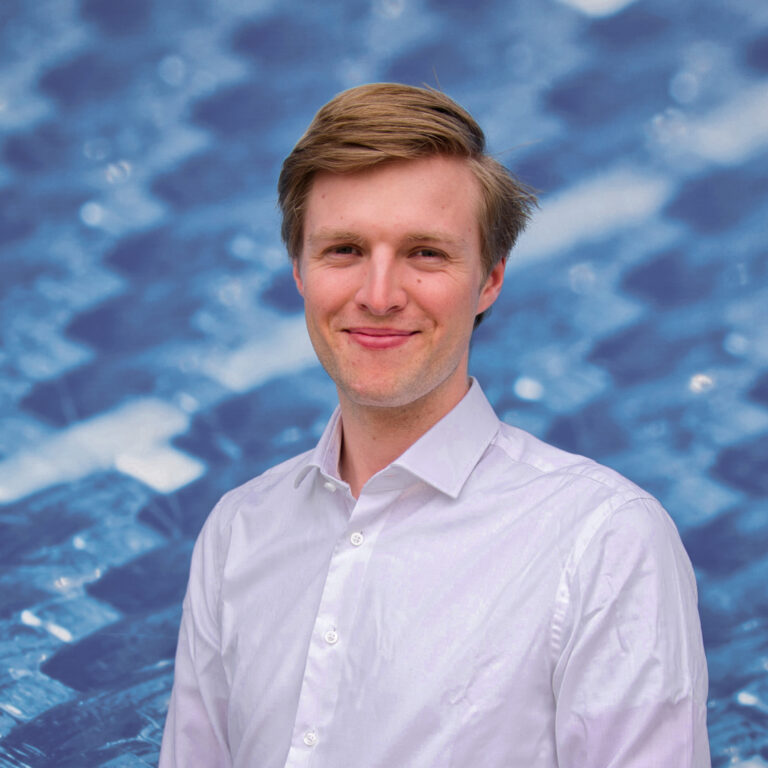
PhD Researcher
Fausto Visser
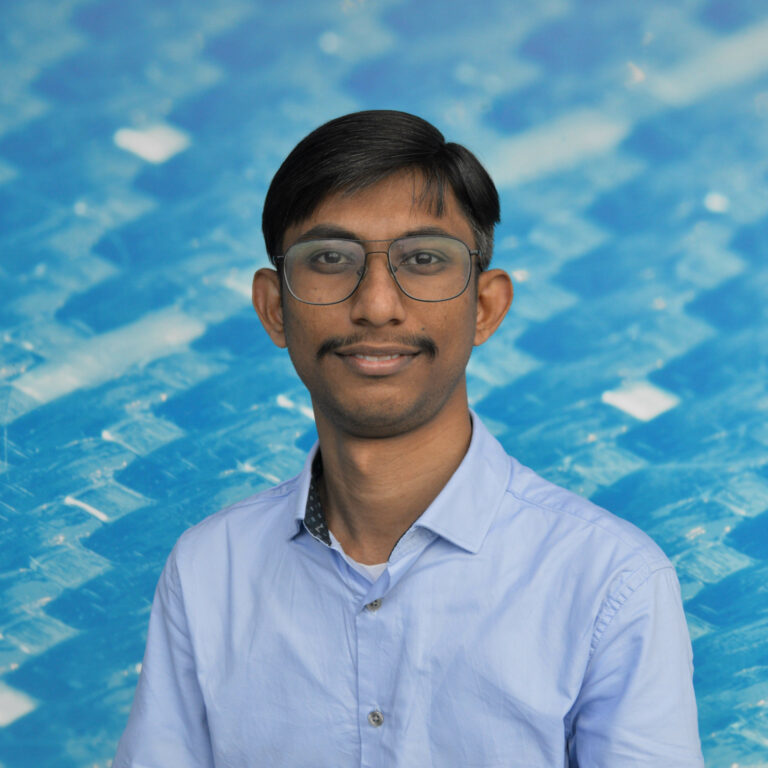
PhD Researcher
Manoj Gongati
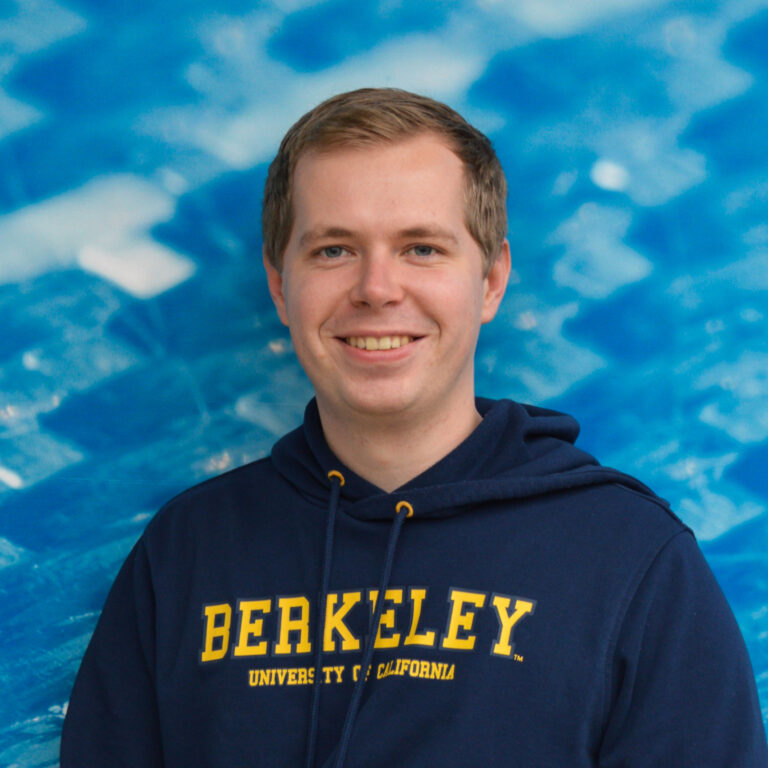
PhD Researcher
Martijn Bos
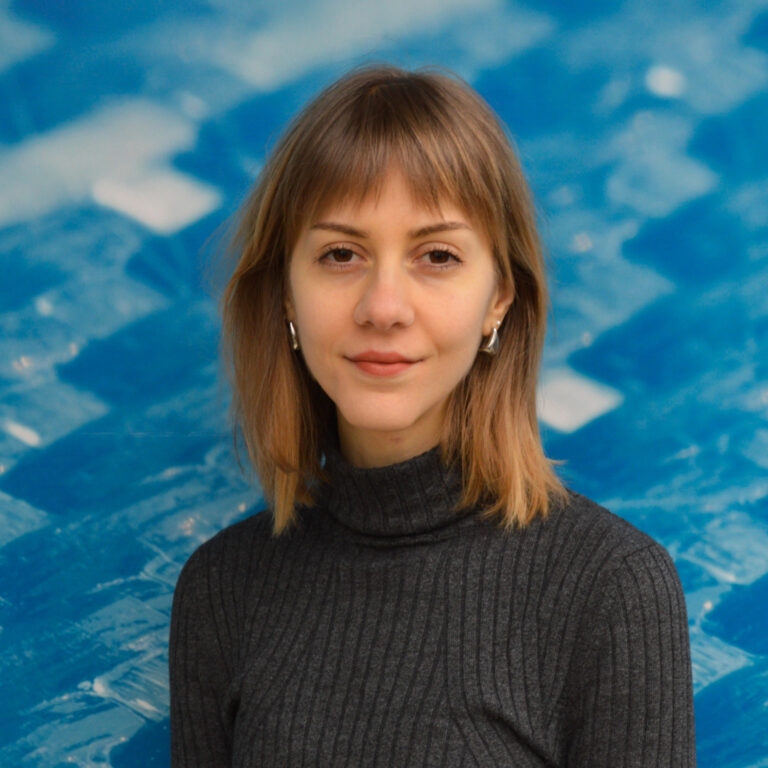
PhD Researcher
Maria Luisa Puga
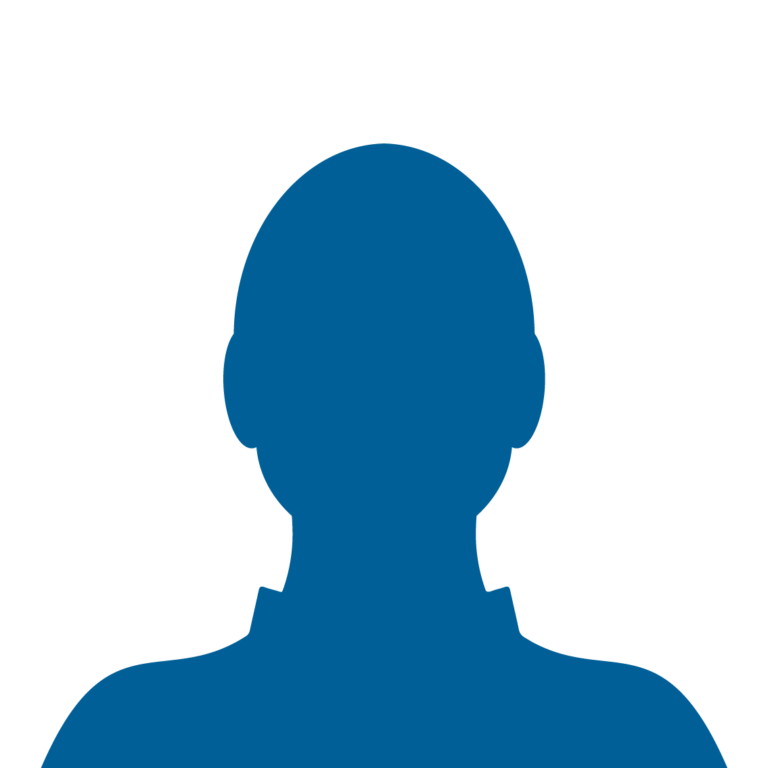
Guest PhD Researcher
Masoume Azizian
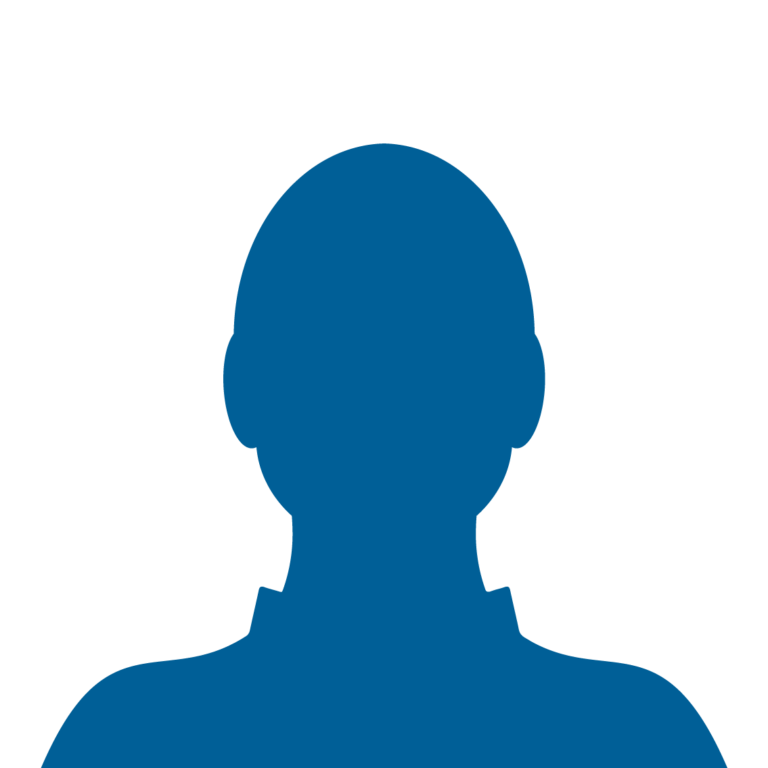
PhD Researcher
Paul Ceralde
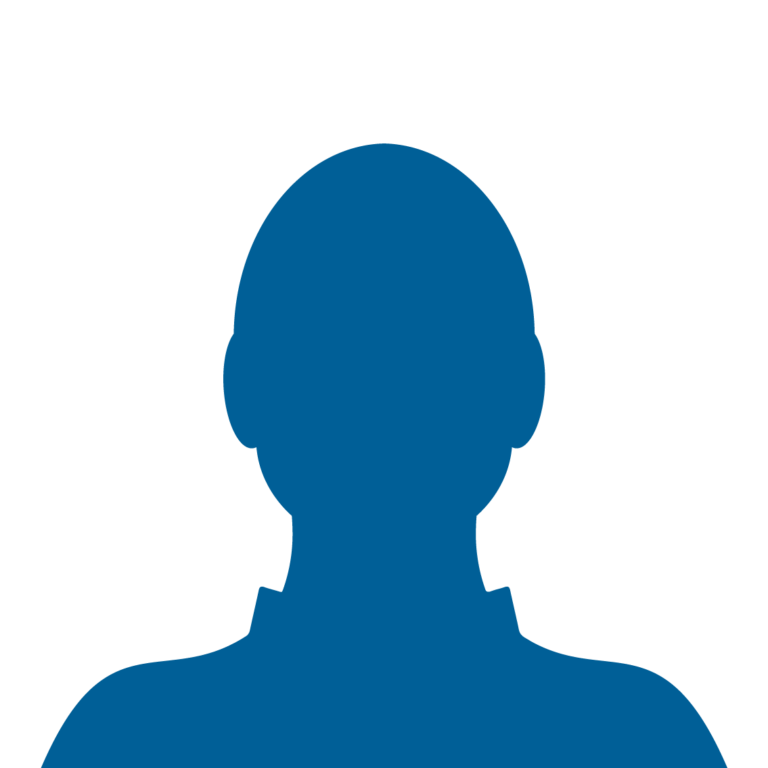
PhD Researcher
Rachel Nguyen
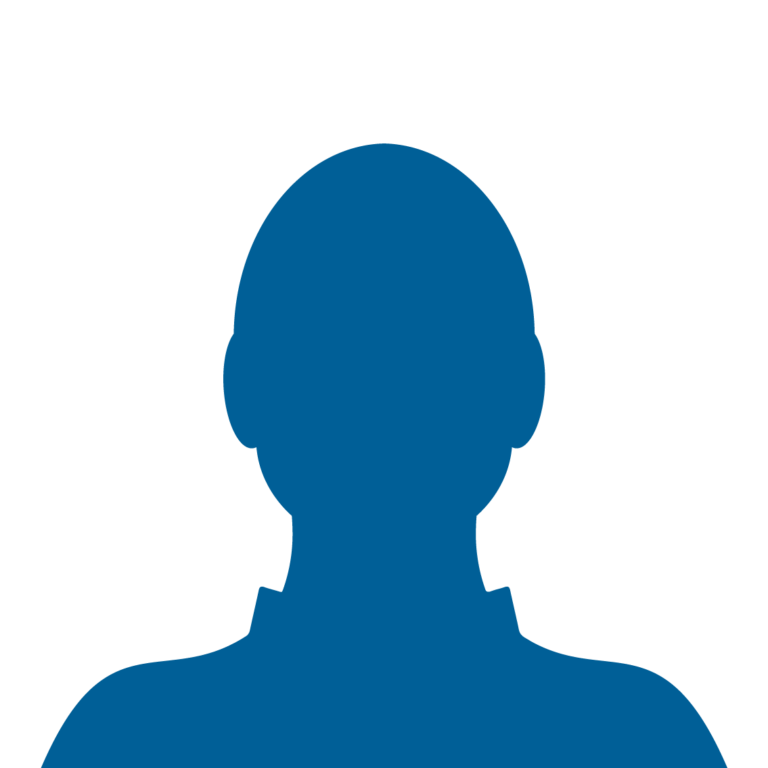
PhD Researcher
Antonio Amore Akiki
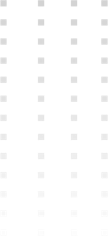